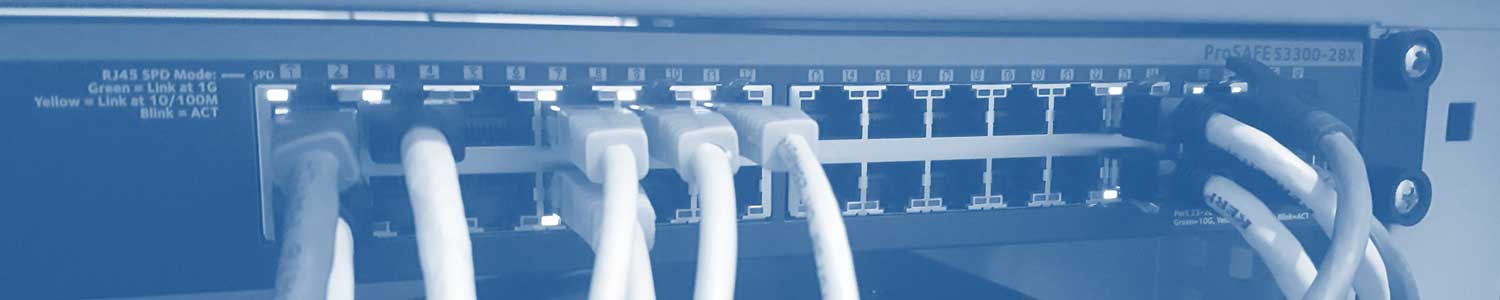
Containment Simulation of Turbomachines
For modern drives such as fuel cells, simulation can ensure that no fragments escape when a compressor or turbine impeller bursts. The so-called containment simulation offers the possibility of investigating a wide variety of burst scenarios. In this way, the housings surrounding the respective rotating components can be evaluated and optimized regarding their retention capacity. Simulation during development also offers an increase in efficiency, a shortening of development times and a high savings potential in terms of costs. This is achieved in development by saving time-consuming tests and in operation by avoiding damage, with the associated consequential costs and loss of image.
Passing the drop test successfully
Dynamic shock loads during transport or incorrect handling can cause damage when products, containers and packaging are bumped or dropped. To protect products and the environment from this damage, effective drop protection is of great importance.
The aim of the requirements in the drop test is to minimise or completely prevent damage to the product and to prevent transport containers and packaging from being opened by force and possible leakage of operating or hazardous substances.
In the simulation, the virtual drop test can be used to examine the shock loads on the products, containers and packaging in detail and optimise the energy absorption. Considering applicable standards and product specifications, weak points can be fixed in advance and design errors avoided. Existing containers and packaging can also be optimised in terms of weight and material, thus saving resources and costs.
Contact us, we can help you to develop your products and their containers and packaging for drop test requirements more quickly and effectively with simulation. This allows you to save time and costs for prototypes and tests and avoid possible damage to the product or the environment later.
Protection of Connections
Snap-fit connections are widely used as a practical and relatively inexpensive connection option. However, despite the existing experience with these components, the connection sometimes fails, cracks or breaks.
This is where simulation can help to ensure the safety and function of the connection. It makes it possible to analyse loads in combination with certain movement sequences, such as in the pressing processes of such snap-fit connections.
Non-linearities of material properties are taken into account as well as the sometimes complex contact situations.
This makes it possible to examine and optimise structures efficiently and quickly. For example, the function and holding force of snap-fit connections can be ensured.
Fan-Blade-Off
In a fan-blade-off test one blade of a jet engine’s fan is blasted off at full speed. In order to receive an approval for the jet, this blade needs to be retained within the casing for one thing and for another the jet must withstand the resulting imbalance. When it comes to costs and development times, these fan-blade-off simulations are essential in today’s jet design as they allow for one single successful qualification test at the end of the development process.
Screws’ pull-out
Screws and bolts are well-known and versatile elements in machine and plant construction. Its dimensioning for the usual operations focusing on fatigue strength bases on guidelines such as VDI 2230. When it comes to dynamic and complex loading of screws leading even to failure, simulation facilitates capturing local and non-linear plastic effects. Basing on a validation of simulation and tests, qualified CAE models allow for dimensioning screws and bolted connections even under extreme loads.
Specimen tests
An accurate material definition for simulation describing the non-linear, elastic-plastic deformation and failure behaviour of the material, requires at least various tensile tests on specimens at different temperatures and strain rates. Results of shear, torsion, bending, and compression tests ideally add to these data. This allows to capture not only the nearly uniaxial loading in tension but also the materials’ deformation and failure under triaxial loads.
Puncture
Highly dynamic loads occur when a projectile or a fragment of a turbomachine’s rotor impacts on surrounding structures or on casing walls. As the resulting loading situations are highly complex, especially in the case of penetration and puncture, material description basing on specimen tests only are no longer sufficient. So puncture tests and ballistic tests using plates enable an extensive description as well as the validation of material models.
FMH / Head Impact
In the automotives’ interior, simulation contributes to vehicles‘ passive safety, too, as it helps to protect passengers from injury in case of an accident, for instance form injury to the vulnerable head area. Legal requirements and guidelines such as FMVSS201 and UN R21 deal with the vehicle’s interior and aim at preventing serious head injuries.
In the vehicle’s interior field, simulation is used for a suitable design of pillars as well as roof structures and it helps to determine the targeted application of clearances as well as of absorbers and deformation elements.
Pedestrian / VRU Protection
VRU protection aims in avoiding or at least reducing injuries of pedestrians, and increasingly cyclists, and all other so-called vulnerable road users (VRU) when colliding with a car. Simulation enables for a appropriate design of the vehicle’s front in order to protect these vulnerable people.
Passive constructive measures mean a targeted configuration of the structural stiffnesses as well as of clearances and absorbers placed below the structures. Active protective measures are an additional tool, comprising for example active hoods or airbags for the windscreen, both increasing the deformation space in case of a head impact before colliding with stiff vehicle components.
Full vehicle
In the development and design of new vehicles a series of legal regulations has to be taken into account, concerning the vehicle’s structural stiffness and its safety. In the case of an accident, a sufficient survival space must ensure the protection of the passengers.
Due to the large number of these legally prescribed tests, such as front, side, rear, and roof impact, crash simulation is indispensable in today’s automotive design in order to guarantee safety economically.
This video shows a simplified side-pole-impact as one example of these mandatory tests. The vehicle is thrown sideways against a rigid barrier, representing for instance an impact onto a tree.
INPROSIM GmbH
Birkenweg 1
64354 Reinheim
Germany
+49 (0) 61 62 / 65 23
www.inprosim.de
info@inprosim.de
INPROSIM GmbH
Birkenweg 1
64354 Reinheim
Germany
+49 (0) 61 62 / 65 23
www.inprosim.de
info@inprosim.de