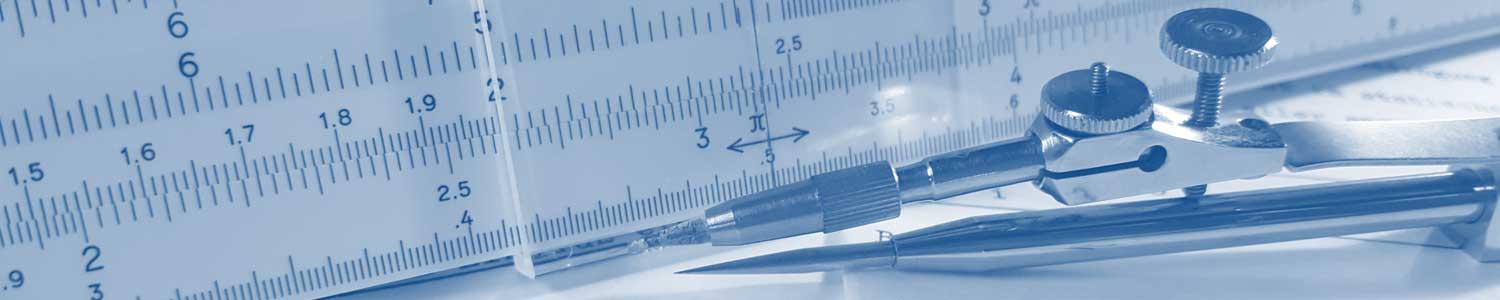
Reproduction of cast housings and screws in containment simulation
14th LS-DYNA Users’ forum
October 10 – 12, 2016, Bamberg, Germany
For turbomachines such as exhaust gas turbochargers stringent requirements apply concerning the containment safety in case of a disk burst. In the engineering of new turbochargers explicit simulation is increasingly used when it comes to product safety. Certain guidelines established as ‘state ode the art’ concerning model assembly and material specification on containment simulation. This talk describes these requirements for typical cast housing components and screw connections. In addition, due to the comparison to a test, it offers an outlook on the validity and predictive power of such qualified simulation models.
Material Model for Deformation and Failure of Cast Iron for High-Speed Impacts
3rd European Hyperworks Technology Conference 2009
November 2 – 4, 2009, Ludwigsburg, Germany
Thick-walled cast housing components are subject to a multiaxial stress state when loaded, that leads to diverse damage up to rupture depending on the load path. Explicit simulation today allows for capturing this failure under triaxiality in highly dynamic loading within commercially available material models. This paper gives notes on capturing the relevant parameters by means of typical specimen tests. Finally, it demonstrates the achieved quality of the material description with a multiaxial failure by a ballistic test with a projectile penetrating a cast plate.
Simulation of a clamping ring under high dynamic loading
7th European LS-DYNA Conference
May 14 – 15, 2009, Salzburg, Austria
Screws and clamping rings are typical connecting elements, well described concerning the technical design for the usual linear-elastic operation by standards, guidelines, and manufacturer specifications. A highly dynamic operation requires for capturing of elastic-plastic effects up to failure by numerical simulation. Using the example of an exhaust gas turbocharger’s strap, this talk offers hints on the meshing strategy for an accurate to the geometry representation of the strap’s relevant elements. Furthermore, it shows the importance of a validation of simulation with tests before integrating these connecting elements into a full model or into an assembly.
INPROSIM GmbH
Birkenweg 1
64354 Reinheim
Germany
+49 (0) 61 62 / 65 23
www.inprosim.de
info@inprosim.de
INPROSIM GmbH
Birkenweg 1
64354 Reinheim
Germany
+49 (0) 61 62 / 65 23
www.inprosim.de
info@inprosim.de